Audio sample provided by Alexander Smith, D. C. Schroth Organ Builders.
Photos by David Schroth and Brian Nichols
We now have available a 1932 Wicks (Re-installed in 1962), including pipework, chests, blower, etc. The organ is currently playable but will be removed in January, after which the console and chestwork will be discarded. Wicks pipework from this period is exceptional, and though the current installation was not entirely successful, we believe a beautiful instrument could be crafted with these voices (including perhaps a few additions).
The current tonal resources which are available (Current and sample stoplists attached):
16′ Principal (Metal) – 56 Notes
16′ Subbass – 44 Notes
16′ Leiblich Gedeckt – 85 Notes
8′ Principal – 61 Notes
8′ Violin Diapason – 61 Notes
8′ Geigen Principal – 61 Notes
8′ Gemshorn – 61 Notes
8′ Bourdun – 61 Notes
8′ Nason Flute – 61 Notes
8′ Salicional – 61 Notes
8′ Celeste – 49 Notes
8′ Dulciana – 85 Notes
8′ Unda Maris – 49 Notes
4′ Octave – 61 Notes
4′ Koppelflute – 61 Notes
4′ Harmonic Flute – 73 Notes
2 2/3′ Twelfth – 61 Notes
2′ Fifteenth – 61 Notes
8′ Fagotta – 61 Notes
4′ Oboe – 61 Notes
4′ Krummhorn – 61 Notes
1922-1962 Wicks – Current Stoplist – D. C. Schroth Organ Builders
1922-1962 Wicks – Sample Two-Manual Stoplist – D. C. Schroth Organ Builders
1922-1962 Wicks – Three-Manual Stoplist – D. C. Schroth Organ Builders
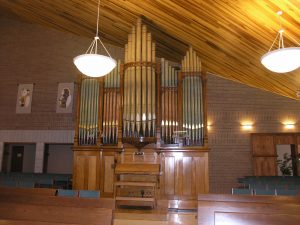
Photo Credit: Patrick Ryan
The 1898 instrument from August Prante was his very last completed instrument before he died tragically in a buggy accident in downtown Louisville. There are only two completely intact instruments from this local firm, though there are several examples of their instruments that were expanded upon. They were a notch above the average as far as the Victorian American instruments were concerned, and this example was boldly voiced.
Though sadly the mechanical components of this landmark tracker organ have not survived, we still have nearly all the pipework, and these broad and sweet Victorian American voices would make a wonderful basis for a beautiful instrument in a mid-sized building. The surviving pipework is as follows:
16′ Double Open, 27 pipes
16′ Bourdon, 27 pipes
8′ Open Diapason, f18-a58
8′ Violoncello, 27 pipes
8′ Violin Diapason, 58 pipes (bottom octave stopped)
8′ Melodia, 58 notes
8′ Stopped Diapason, 58 notes
8′ Gamba, c13-a58
8′ Dulciana, d15-a58
8′ Aeolina, c13-a58
8′ Trumpet, 58 notes
8′ Bassoon/Oboe, 58 notes
4′ Principal, 58 notes
4′ Violina, 58 notes
4′ Flauto Traverso, 58 notes
4′ Flute d’Amour, 58 notes
2′ Octave, 58 notes
2′ Piccolo, 58 Notes
We have put together two sample stoplists below as an example of what could be made out of such a collection. We’d love to find a client who would like to have this pipework as part of a commitment for a complete organ. To that client, the pipework would go free. We’d be willing to negotiate the sale of the pipework if no such commitment were made.
We have taken possession of the pipework from a three manual Kilgen–Opus 7504 from 1926, and would love to find these pipes another home. This organ, with it’s full diapasons, lovely strings, and beautiful wood flutes, would make a wonderful basis for an organ in a mid-sized congregation. The original chests were damaged and have not been retained. The pipework lists as follows:
16′ Major Bass
16′ Bourdon
8′ Open Diapason
8′ Violin Diapason
8′ Gemshorn
8′ Melodia
8′ Stopped Diapason
8′ Fern Flute
8′ Gamba
8′ Dulciana
8′ Unda Maris
8′ Salicional
8′ Celeste
8′ Trumpet
4′ Octave
4′ Geigen Octave
4′ Zart Flute
4′ Harmonic Flute
2′ 2/3′ Nazard
2′ Superoctave
2′ Piccolo
Here are two sample stoplists to help give an idea of what could be made from all this:
Three Manual – Kilgen Opus 7504
Two Manual – Kilgen Opus 7504
The pipes could go “free” to a client who initiates a contract for installation from D. C. Schroth Organ Builders. Parties seriously interested can reach out via our contact page.
We would be happy to negotiate the sale of the pipes directly (no installation). Simply reach out via our contact page.
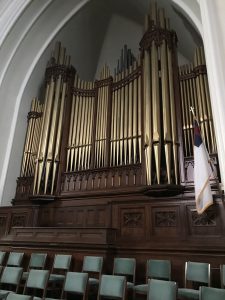
III/57 Austin Op. 2480, Walnut St. Baptist, Louisville, KY
The scope of what will be written will hopefully help those blessed with a pipe organ in their care to make more informed decisions about how to have it cared for long term. We offer here a list of five things that will answer the most common questions we receive on this very topic.
1.) Form a positive relationship with a good organ building firm: This seems like a logical first step, but is also critical for establishing a stable and efficacious plan for keeping the instrument in good working order. A good firm, staffed with personable and knowledgeable builders, can adapt to the needs of each of the instruments in their care to deliver diligent service and provide insight and guidance.
Of course, it is wise for a venue to be very careful about who they entrust with this responsibility. There are many skillful craftsmen in the organ-building trade. It is certainly not unreasonable, considering the magnitude of investment represented in any pipe organ, to interview a prospective firm prior to making any commitment, to ask for references, verify insurance, and even to view other work that firm has performed, especially if it is likely they will be called upon to perform major work in the future. The level of competence of a prospective builder should be considered above all other considerations, as poor decisions can mar a fine instrument permanently, or cause other problems that will negate any perceived monetary savings by substandard work. The mechanics of organ building are simple to learn; the philosophy required for good execution of the craft takes years to develop.
Also, selecting a firm that is easy to communicate with, and who keeps a professional regard to punctuality, will save substantial headache. They should feel that their organ builder has “got their back” when they need them. Aside from being a competent craftsman, a good service professional knows that “without clients there is no craft,” and will strive to prevent abuse by way of being unreasonably tardy in appearing to appointments or delivering work. We are always astounded, when meeting new clients, at how much of this abuse a venue will tolerate before considering alternatives.
It may be that a suitable builder will need to be brought in from another city. Though the perceived expense of travel may seem prohibitive, often that builder will already have several other clients in the area which will make this much more reasonable.
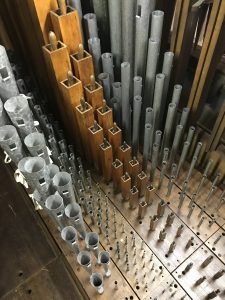
Swell division of the III/37 Farrand & Votey Op. 714 (1894), St. Martin of Tours, Louisville, KY
2.) Work with your organ builder to set up a plan: Once sufficient consideration has been given and a firm is selected to be the organ’s custodian, an appointment is usually made to assess the organ. We often include this in our first tuning, and all known or potential issues are recorded. Regardless of the financial status of the client in question, the client should know of any problems with their instrument, and their builder should work with them to help them understand the level of importance and financial commitment required for each item, even if they will not be remedied right away.
Beyond this, builder and client should discuss frequency of tuning and service visits. Our firm resists the temptation to fit each client into a box, instead discerning the client’s needs and forming a plan that best fits their needs and that of their instrument.
As service visits come and go, the builder should keep a lookout for potential issues and record them for the client. Our Service Analysis explains what was accomplished during each visit, details what issues were not addressed, and re-iterates any outstanding issues so the client understands they have not been remedied.
3.) Keep good records: It is always a joy when clients pull out a complete dossier of records on their instrument, especially if the instrument is historic. In the best situation, this information can be used to make informed decisions concerning tuning, or for restorative work. On the other hand, we have experienced instruments where detrimental revisions were made, and lack of records prevented a clear picture for returning the instrument to proper order.
Also, modern technology makes it very easy to record very accurate pitch and temperature data, and since these two factors are critically important to maintaining stable tuning, we record them on each Service Analysis, and reference these documents during each subsequent tuning. That way, we can be assured that the tuning is being done correctly each time.
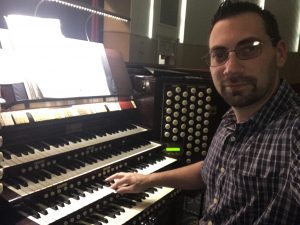
David Schroth Jr. at the console of Pilcher Op. 1454, Louisville Memorial Auditorium
4.) Be conscious about environmental considerations: The pipe organ is a “living, breathing” entity, and responds to the environmental changes it is subjected to. Making deliberate decisions on temperature control in the building will help stabilize tuning and can add years to the life of the delicate woodwork and leather in a pipe organ. See our guide Temperature and the Pipe Organ for more detailed information on this topic.
5.) Get your congregation excited about the organ: When we explain our vocation as pipe organ builders to people “on the street”, we are nearly always met with fascination and excitement. In a world brimming with technology, the reality of the pipe organ as something more than just a pretty display of gold pipes is something many have overlooked completely. Many churches have inherited these treasures, a direct result of the stewardship of their forbears, and the artistry of some of the most highly-trained craftsmen in the world. We can easily ensure that these instruments will continue to be passed down by making people in the pew aware of the beauty and craftsmanship of the instrument, and by involving them in understanding what is required to keep them in top shape. We love to work with a congregation that is proud of its pipe organ, no matter how big or small, especially since they are usually happy to see us keeping it in top shape!
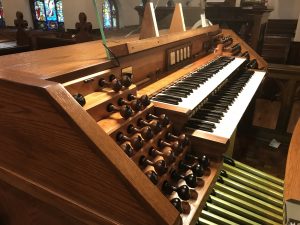
St. Marks Episcopal, Louisville, KY; Console reconfigured for drawknobs 2017 by D. C. Schroth Organ Builders.
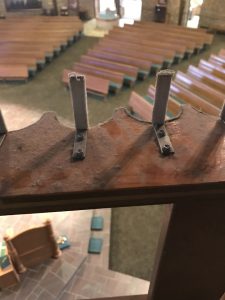
Facade racks covered with dust
Those of you who follow our Facebook feed have most likely seen our recent posts of our organ cleaning project for St. James Catholic Church in Elizabethtown, KY. Though a small instrument, the organ at St. James had accumulated much dirt and debris over its forty-year lifespan, and we encouraged the parish to have us clean the organ. Taking this to heart, we were commissioned to perform this task, and it was executed in a four-day session which resulted in a significant improvement to the chambers and pipework that will help not only to keep our crew from looking like chimney-sweeps, but which will aid in the stability of the tuning and speech of the instrument.
Allow us to further explain: Organ pipes are made to direct a
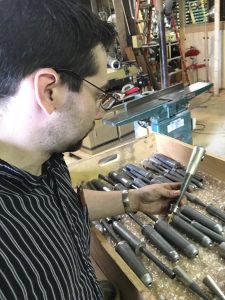
David Schroth Jr. inspecting the Trumpet before cleaning
fine wind sheet in such a way that the agitation thereof against the upper lip sets the air column inside the body of the pipe in motion, resonating a tone. Through the delicate voicing process, this tone can be changed in very subtle ways to produce exactly the quality of tone desired. As dust settles into the pipe, it can (especially with smaller pipes) begin to have an influence on the tone, and can make tuning or speech unstable. In a case where there is clearly debris in a pipe that is not behaving, we can often set a pipe aright merely by blowing the dust out. Thus, it is advisable, especially in buildings where significant dust tends to accumulate, to have the inside of the organ cleaned by organ specialists as the need arises.
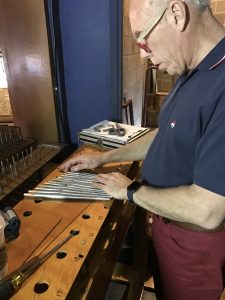
David Pilkinton laying out cleaned Gemshorn pipes for installation.
In addition to merely cleaning everything in the organ, this gives us the chance to correct issues in the instrument which go beyond the scope of regular maintenance, especially since removing the pipework often gives us better access to the innards of the organ.
In so doing, we effectively return the inner part of the chamber, and the pipes, to the same condition as when they were brand new. We also take the time to go through the speech of all the pipes and make sure all are speaking well and proper. In the case of the organ at St. James, this regulation had been badly needed for quite awhile With the pipes free of debris and other issues corrected, we could perform this basic regulation, knowing that these minor corrections will hold into the future, bringing a new level of stability to the instrument.
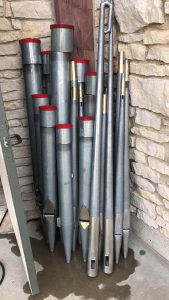
Newly-cleaned zinc pipe basses
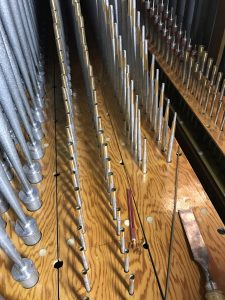
Gemshorn and Erzahler pipes in their newly-cleaned racks
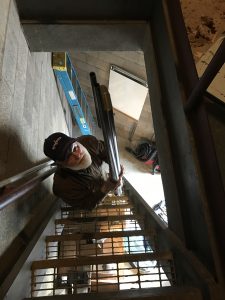
James Forsee handing pipes up into the chamber
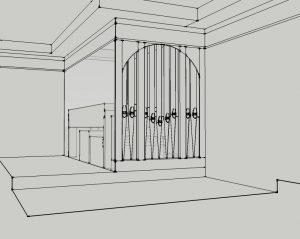
3D Rendering of the proposed organ case, in the rear gallery.
Over the past two years, we have been working with Our Lady of the Pillar Chapel in Louisville, KY to formulate a solution to install a small Wicks instrument that was donated to the church. We have entered into an agreement with the venue to begin work on the project, and this is a project that promises, despite some challenges, to be a wonderful addition to the community at Our Lady of the Pillar.
The chapel of Our Lady of the Pillar is dedicated to the exclusive celebration of the Tridentine Liturgy of the Catholic Church. With an emphasis on chant and traditional hymn accompaniment, we were tasked to provide an instrument that would support, though not overpower, the choir, which is a particular challenge in this room, given some of its acoustical properties. The balcony in the intimate chapel extends nearly one-third of the way into the space, and the floor is slanted down towards the sanctuary, these two factors creating an overpowering “live zone” in the sanctuary itself. Thus, a balance will need to be struck to allow the organ to bloom naturally and tastefully into the room, without overpowering the celebrant during liturgical functions.
The instrument itself is a typical example of a small instrument from the 1960’s, containing five ranks as follows: Diapason, Flute, Salicional, Gamba, Orchestral Oboe; most of these unified in the usual manner. The Diapason is scaled larger than one would expect for a small instrument, and the strings smaller. Some judicious rescaling and logistical corrections within the instrument will take this limited instrument to a new level of versatility which should serve the liturgical necessities well.
Please stay tuned as we plan to provide updates as this project unfolds!
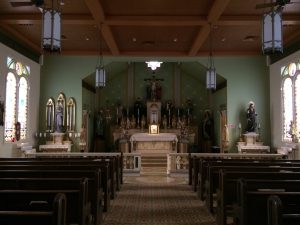
The sanctuary of Our Lady of the Pillar Chapel

First Presbyterian Church, Austin, TX. 1900 Moller Tracker
A
s we sit in our hotel in Austin, TX, waiting to return home after having recently completed a very successful collaboration with C. Bobsin Organbuilder in San Antonio, TX, we wanted to share with you some of the joys and sorrows of the project, in hopes that something positive from the experience can leak out of our minds and into the organ-building milieu of our time. As you will come to see, what we have accomplished was nothing revolutionary, but we hope the principles we encountered may be able to assist our colleagues in some way.
The Victim
Our patient in this project is a 1900 Moller, First Presbyterian Church, Austin, TX, original to the congregation, but moved in the 1960’s to it’s new home in the Mesa suburb. Quite a list of builders had their hand in making alterations to the instrument, with mixed successes. As occurs with many instruments from this time period, the larger 8′ stops were replaced with upperwork, and the instrument was given a German-eclectic tonal flavor, which sounded well into it’s small yet pleasant acoustic.
Coming onto the scene in July 2015, we weren’t sure what to expect. A grandiose new console by Bobsin and crew had been installed, and it was time to turn serious attention to the key action, which was exceedingly heavy. Initial measurements were unable to be made, since the key action weight exceeded the limits of our usual key gram-meter!
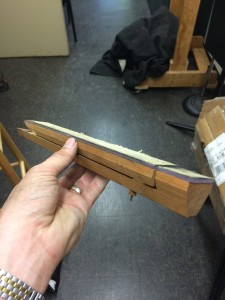
The original bass manual pallets.
Our Initial Observations
Perplexed, yet not surprised by the heavy key touch, we sought to determine the root causes of such, so that a reasonable solution could be concocted, while keeping the tracker action intact. As we began poking and prodding, we found the action in bad need of general adjustment, this not having been done in some time. This involved ensuring that all squares and roller arms are ninety degrees to the action when they are half-way through their travel (not in the resting position, as is a common misconception) to provide maximum travel of the action and prevent binding. Performing this adjustment in itself made a noticeable difference, though not enough to satisfy the ultimate goal.
Once the action was well-adjusted, we were able to pinpoint non-ideal conditions in some of the intermediary action transfers, particularly in the Great. As a result, we built a new square rail that improved these conditions, particularly by eliminating whipping of the tall vertical trackers, and also by creating backfalls that were able to be easily geared to change the ratio of key depth to pallet drop.
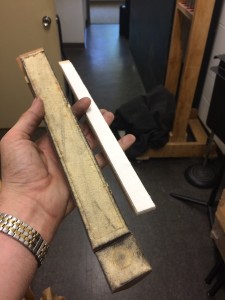
New pallet (right); Old pallet (left).
Gearing is a common way to reduce key weight. If you realize that there are two main forces involved in a key action: tension from action weight/friction + pallet spring, and pluck, you can see that reducing the amount of pallet motion, for instance, in half in this case (2:1), reduces the amount of weight at the key from the pallet roughly by half. Somebody had been smart enough in a former rebuild to drill holes in thee Swell backfall squares to allow this, so the Swell was already geared out 2:1 when we arrived. (That being said, they didn’t adjust other things such as the tracker guide combs, so this resulted in binding). Our new backfall for the Great would allow us to gear the action in three positions: 1:1, 2:1, 3:1. We found that the action was nearly acceptable when the action was geared to 3:1, however, the speech point was then so far lowered on the key that it made playing uncomfortable.
In the pallet box, where we expected over-sized pallets, as was typical from this time period, we found that things exceeded our expectations. As was typical, the pallets were the full width of the channels, which in the bass were a hefty 29mm wide! In addition, old, stiff leather was causing sealing problems, which had been alleviated in the past by adding tension to the pallet springs which, as one can imagine, exacerbated the heavy key touch problem. In addition, the Moller pallets had a type of “balancier”, which is an added mechanism that uncovers a small hole in the channel, equalizing the pressure so that the pluck was then reduced for the large pallet. While this seems like a clever idea, the added mass of the mechanism, in addition to the lost motion in the balanciers, made the basses heavy and mushy feeling.
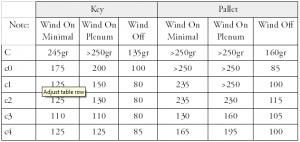
Initial Great Key Tension Data
Thinking Through the Problem
Our immediate conclusion was that the pallets were too big, and we needed to make the pallet openings smaller. But how? This was the million-dollar question. Due to situations beyond our control, removing the chests was not an option. Whatever solution was applied needed to be implemented with the chests in situ. We took extra care to think through each step of implementing this so that we would not run into any problems that would be caused by working within the deep, short pallet box. Considerations for access and installation led us to follow the advice of a colleague who recommended shimming the channels to reduce the slot width.
So then we needed to know how much we could reduce the pallet slots by without causing wind problems in the channels. First, we gathered the necessary data on our end by adding together the windways of all the pipes on the channels (we used the C’s). We consulted with two well-known builders, who graciously provided us with their own formulas for figuring pallet openings, pallet drop, etc. We also came across a wonderful essay on the subject by Colin Pykett (http://www.pykett.org.uk/calculating_pallet_size.htm). Pykett had produced a series of controlled experiments to find out how large exactly a pallet slot needed to be, not only to provide enough wind at a stable pressure, but to do so under varying loads, to prevent “robbing” of wind from mixtures, etc. I suggest that anyone needing to scale pallets absorb this data. We found that his data indicated larger pallets than that dictated by the formulas provided by our colleagues, and since our calculations revealed pallet openings that were already significantly smaller than the originals, we stuck with the larger formulas.
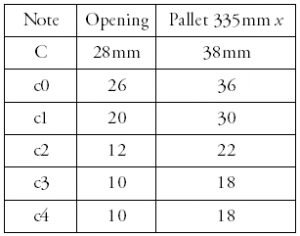
Original Pallet Scaling
Pykett’s data also included information on pallet drop, especially compared to the width of the pallet.
The consensus from Pykett and our colleagues was that the pallet should drop half the width of the pallet. Since our current pallet drop with the action geared 2:1 was 5.5mm, we made the bass pallets 12mm, and kept the treble pallets 10mm.
Of course, these were still generously scaled according to our calculations. So we furthermore reduced the area of the pallet opening by inserting blocks in the back of the pallet slots. (We only performed this second operation in the Great).
We made new pallets out of basswood, in the same style as the originals, which curiously have no tails, but pivot on the leather. This allowed us to keep the back pins in-place for re-use, and we were able to use the original spring-loaded tail hold-ups in the treble. The balancier holes were covered with a membrane, and the new pallets have extensions to carry the motion to the original pull-downs. The original pallet springs were straightened and re-used.
We were able to regulate the pallet tension to max 125gr at the pulldown, without any problems with repetition or sealing. The Great and Swell were geared back to 2:1, and the key tension at the key is now about 125gr, and very pleasant to play. There is no detectable robbing of wind when larger stops are added.
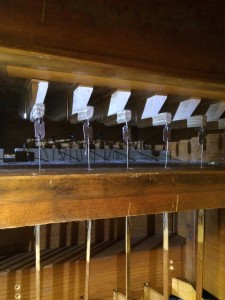
New Bass Pallets Installed in the Great
Closing Considerations
In the end, one of the caveats of this project was the fact that the major wind-hungry stops had been replaced with upper-work. If the organ’s stoplist had been original, such drastic changes would have been reduced by necessity.
We also have vowed never to perform this operation again without taking the chests out. Though we were able to reduce the amount of necessary work inside the pallet boxes through careful planning, the operation was still extremely difficult, and took an exorbitant amount of time to produce the high-quality results necessitated for this precision operation. In the future, in a non-historic instrument, we would most likely opt to remove the chests and install a new pallet board with routed slots.
I realize the fine details of this project are too exhaustive for a blog post. If anyone has any questions about this procedure, please feel free to ask!
In our several years in the organ service field, we have come across many instances where misunderstandings or lack of information concerning the temperature needs of a pipe organ have caused frustrating situations. We feel it is good to brush up every now and then on the principles involved, in hopes that a more complete education on the topic can help foster a better musical experience with an instrument. With that in mind, I present this “primer” of sorts with just that intention.
Of all the considerations one makes in the design and eventual stewardship of the “king of instruments”, stability should be a prime consideration. Just as an airline pilot depends on his controls working perfectly every time, so too an organist depends on his instrument behaving itself predictably so that together they can smoothly execute the musical ends they serve. Just as the skills involved with building an aircraft must be informed by science, so too must an organ craftsman or technician be informed by the scientific principles at work.
One of the greatest causes of instability, as we have found in our service experience, is the issue of how an organ interacts with its environment. Organ technicians know that an organ is a “living, breathing” entity, and responds sensitively to changes in temperature and humidity. We try to encourage venues to improve the environmental situations to be favorable to stability in the organ, and we believe that doing so will not only improve their experience with their instrument, but will save them money in the long run. We will attempt to impart some of the principles involved by way of answering common questions that come up in the field:
At what temperature should the organ be tuned?
When we come to tune, and especially when we come to tune a new client’s organ, the first thing that must be determined is the pitch of the organ. Less important than the actual number is the relationship between the pitch and the temperature when the organ is tuned. Standard orchestra pitch is A=440Hz, and the organ usually gets pitched so that tenor A on a 4′ stop =440Hz at the ambient room temperature of 70ºF. As the temperature goes up, the pitch rises, and as it falls, the pitch lowers.
Reed pipes like Trumpets and Oboes rise and fall at a slower rate than flue pipes. This is why it is so important that the tuner knows what the proper tuning temperature is in the room, and that the room is stabilized at that temperature when the organ is tuned. It is also important that the room be brought within two degrees of that temperature when the organ is used in functions, to ensure proper tuning. (Playing the organ at lower or higher temperatures will not damage the organ, but the tuning, especially between the reeds and the flues, will be sour).
It is often the case that factors have caused the normal occupied temperature of a room to change, from one tuning to the next. Our firm can easily catch this when we arrive, as we can verify the previous tuning temperatures through our service records. We try to determine if changes have occurred prior to our often long journey to a tuning, so we can advise and plan accordingly. More often than is desirable, we only learn of such a change when we arrive. Depending on the individual scenario, the outcome can vary from carefully proceeding with a tuning (which always involves more time) to having to reschedule.
We always recommend that clients make an informed decision about what the occupied temperature should be in their venue and stick with it. Lock boxes can and should be installed over thermostats if there is a risk of the uninformed changing the temperature.
How long before a tuning must a room be brought to proper temperature?
The above being said, arriving to a room which is not stabilized at the determined temperature will always result in us leaving without tuning. By stabilized, we mean the following:
-
The heating or cooling system is no longer working to bring the temperature up or down, but is only running to maintain a constant temperature in the room, or “floating”
-
The organ chambers, which should only be heated or cooled passively, have had time to stabilize to their determined temperatures
We usually recommend the room be heated/cooled at a minimum of four hours from a fallback temperature prior to a tuning, to give the room time to stabilize. Especially true with heat, certain types of HVAC systems will in effect overheat the air in the room initially, especially higher in the room where the hot air is artificially forced. This will even out as the room temperature rises and the air mixes, especially if there are air circulating devices in the room (ceiling fans, erc. . .) Even though the thermostat will display the correct room temperature, the heat has not had time to properly dissipate throughout the room, and the organ will be a mess.
Our firm always takes stock of the pitch and temperature of the divisions of the organ for every tuning. As a result, we can absolutely tell when, for instance, a venue waited until the last moment to adjust the temperature for the tuner. Though we are assured that these occasions were well-meaning attempts to save money, the reality is that we are not able to provide service under this condition. We do our best to turn these situations into educational experiences.
Practically speaking, tuning an organ in an un-stabilized temperature situation will always result in a poorly-tuned organ. We have witnessed well-meaning technicians attempt to “reconcile” things in this scenario, and the results were less than satisfactory (meaning, they were called back to fix the mess once things stabilized).
If there is any doubt as to how long the room needs to stabilize, our firm offers a temperature analysis using temperature-logging devices that can track temperature changes over time, which will give a very informative picture of what is going on in the organ chambers. With this data, we can discuss changes that need to be made, which could involve adding insulation or air circulation, or something as simple as making adjustments to the thermostat at particular times.
Watch Those Programmable Thermostats!
I must digress here from the format to address this point emphatically. Over the past five years, we have witnessed an increase of a disturbing trend where our clients had every intention of providing a well-stabilized room, having set the thermostat back the night before, only to have their settings overridden by the thermostat programming. This is usually not discovered until our arrival, and much to everyone’s horror. And there is nothing to be done but try to either wait or reschedule, if possible.
Must the Room Temperature Remain Constant for the Organ?
One of the most frequent questions we receive is whether the organ requires a constant temperature or whether the room temperature can be set back for efficiency’s sake. The first principle at play is that, barring extremes of temperature or humidity in either direction, the room temperature can be set back a reasonable interval when the room is unoccupied, as long as sufficient time is given to allow the room to stabilize at the tuning temperature before events. So if the organ is tuned at 70ºF for Sunday services, and the room is set back to 65ºF during the week, the organ should be well in tune when the temperature is brought back to 70ºF the following Sunday. How far back to let the heat or a/c slip without affecting stability is a well-debated topic. Though the flues and reeds will generally float up and down without a problem, a drastic change in temperature may alter the relationship of the speech parts of the pipes, especially in the reeds, and may cause them to be out-of-tune or off-speech when the temperature is returned. It may be well to consult with your tuner to discuss this, and to experiment with this in your particular room, under close observation. Of course, the greater the interval between the occupied and unoccupied settings on the thermostat, the longer the room will need to stabilize at the occupied setting. Many of our clients have actually found that greater efficiency is actually achieved by limiting this interval, as it is surprisingly often more efficient to maintain one temperature than to let the temperature float back too far, resulting in an often long “catch-up” period that can offset any savings.
Of equal concern, however, is the effect of humidity on an organ relative to the temperature. Most of the large parts of an organ (chests especially) are made with wood, which swells and compresses as the humidity changes. These wood parts are especially affected over time by dry conditions, brought about by artificial heating. Leather is also affected by humid conditions. These are often exacerbated by the fact that organs are often mounted higher in a building, where the temperature is even higher, and the relative humidity swings are more exaggerated. If the air in the room is not humidified in the winter, it is probably best to allow the room temperature to fall back, to reduce the usual plunge of the relative humidity of the air. Air circulation systems can also help mix the very hot air at the top of a tall building, and reduce the “bandwidth” of stratification between the higher and lower portions of a room. Air conditioning is less of an issue as far as humidity is concerned.
Also, while carefully-placed chamber humidifiers may provide marginal help, the most ideal scenario for overcoming winter dryness is a humidification system that humidifies the air in the whole room. This will not only help the organ, but will also extend the life of any other musical instruments, such as a piano, or any wood furniture present.
Air Flow Around the Organ
As I mentioned, circulating air through the room is generally a positive. One must, however, keep in mind a couple principles that involve moving air around an organ:
-
No moving air should be focused directly into or towards the organ – this includes vents and fans
-
Ceiling fans should not be placed in close enough proximity that they interfere with the sound of the organ.
One caveat to this is that sometimes it is necessary to add a circulating fan to focus ambient air into an organ chamber that has “dead spots” where the temperature will not mix properly. These fans should turn off when the organ comes on. Good case and chamber design can mitigate this necessity. Also, any circulation devices should be installed in close consultation with your organ service company.
Lights Around the Organ
It should also be noted that any lights mounted around the organ will give off heat and affect tuning. We recommend these stay on during tunings. An increasing number of our clients are switching to low-heat bulbs, such as LEDs, which will greatly minimize this effect.
Summary
In summary, here are the most salient points from the above:
-
Always have the temperature stabilized in the room before tunings (at least four hours)
-
The temperature used for tunings should be pre-determined, and should coincide with the occupied temperature of the room in question
-
The temperature can be set back a few degrees without changing the tuning, as long as sufficient time is given to allow the room to stabilize at the occupied temperature for events.
-
Low-humidity conditions should ideally be mitigated
-
The organ chambers should be heated passively from the room, and there should be no vents or fans blowing directly towards the pipework.
In closing, I hope this has helped to convey the basic principles involved in the interaction of an organ with its environment. Putting these principles into practice should help to create a more stable tuning situation. If it seems like changes to your venues’ environment are necessitated, we always recommend including your organ service technician in the conversation.
On behalf of D.C. Schroth Organ Builders, we wish you a most blessed and happy Easter! The Schroth family has another reason to celebrate. Last evening, we brought our beautiful little daughter, Heidi Elizabeth, into the world. She was a healthy 9lbs. 8 oz and 22 inches. Mama and baby are doing wonderfully well.
There may be some true organ-building potential in this little one, as she waited an extra week and a half for Daddy to finish his busy tuning season before making her appearance. 😉 🙂